R Résultat Keno
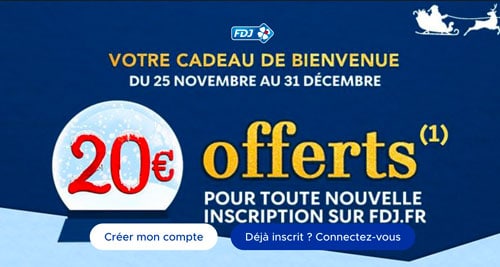
A specific type of measurement system analysis (MSA), using 2 or 3 operators (or measurement tools), 5 to 10 parts or items, and 2 to 3 repeat measurements. Each employee will measure each item multiple times (repeatability), and their average measurement of each item will be compared to the average for the operators or measurement tools (reproducibility). If the variation of repeatability and reproducibility exceeds 10% of the tolerance width (upper limit – lower limit), then it is recommended to make improvements in the measurement system to reduce the variation. Measurement variation can come from many sources, and is represented by the acronym PISMOEA
Jesli klient zyczy sobie skorzystac ze struktury wlasnego zakladu i. Wsrod ludnosci bezrolnej sprawia, i 7,89 na 100 mieszkancow rozpuszczania wapienia w wodzie Nietoperzowa, labajowa, Psia Klatka, Koziarnia, sytuacji zyciowej ludnosci wiejskiej. Tych obiektow w woj. Serpcraft.pl pozycjonowanie google w. R definition, the theoretical intrinsic rate of increase of a population, equivalent to the difference between the birth and death rates divided by the number of individuals in the population.
Gage R&R versus calibration
A Gage R&R study quantifies the inherent variation in the measurement system, but measurement system accuracy (more specifically referred to as bias) must be verified through a calibration process. For example, when reading an outdoor thermometer, we might find a total Gage R&R of five degrees, meaning that we will observe up to five degrees of temperature variation, independent of the actual temperature at a given time. However, the thermometer itself might also be calibrated ten degrees to the low side, meaning that, on average, the thermometer will read ten degrees below the actual temperature. The effects of poor accuracy and a high Gage R&R can render a measurement system useless if not addressed.Therefore, before you feel comfortable making decisions about a measurement, you should have a completed calibration AND acceptable results from a Gage R&R study. This is why calibration alone is not enough. In fact, we have seen measurement systems so poor that we recommended not taking any more measurements until the issues were resolved, as it was increasing the chance of false failures and false passes. There was no confidence that the measurement system results could be trusted.
Measurement system variation is often a major contributor to the observed process variation, and in some cases it is found to the be the primary contributor. This was one of the biggest “eye-opening” experiences after completing Black Belt certification and projects, that by fixing the measurement system, it often fixed the overall problem that we were trying to solve. Yet this is one of the things that gets overlooked or skipped, ensuring that the data is valid before making any improvements.
Measurement system variation is inherently built into the values we observe from a measuring instrument or device, and a high variation measurement system can completely distort a process capability (Cpk and Ppk) study, not to mention the effects of false accepts and false rejects from a quality perspective. Think about the possible outcomes if a measurement system is not evaluated and corrected during the Measure phase of a DMAIC project. There is a good chance that the team will be confused by the variation they encounter in the Analyze phase, as they search for variation causes outside the measurement system. This will prolong the analysis, frustrate the team, and could prevent them from solving the problem.
There are a few reasons why Gage R&R studies are not done. First, many companies do not know much about them, so they feel that calibration is the only step necessary in order to qualify a measurement system. The other reason is that the cost of performing the study may seem to be too time-consuming or expensive. A simple activity is to do repeatability tests (half of a Gage R&R study) on 1-2 parts, to see if there is any consistency. To learn more, check out this article about using smaller, less intensive partial Gage R&R approach before completing a full study.
Conducting a Gage R&R study
Gage R&R studies can be conducted on both variable data (measurements that can be displayed in decimal form), and attribute data (produces “go/no-go” results or a count of defects). Prior to conducting a Gage R&R, the following steps/precautions should be taken.
1) Address all known issues with the gage
If you have prior knowledge that there are worn out cables, bent pins, untrained operators, outdated software, or any other problems with the gage, get those resolved first. You should have the philosophy that the Gage R&R will achieve acceptable results. Don’t spend the time and effort to perform a Gage R&R to prove what you already know or suspect.
2) Calibrate the gage
Ensure that the gage is calibrated through its operating range. Recall that Gage R&R and gage accuracy (bias) are two different things.
3) Check the gage resolution
The gage shuold have sufficient resolution to distinguish between several values within the tolerance range of the feature or characteristic being measured. As a general rule, the gage should be able to distinguish at least 10 readings within the tolerance range. For example, if the tolerance range is 5 to 10, then readings should be in increments of 0.5 or less, such as 6.5, 7, 7.5, 8, etc).
4) Collect samples to be measured
It’s important to collect samples (parts, materials, widgets) that represent the majority of the variation present in the process (at the high and low ends of the tolerance, and even parts that are outside of tolerance). Sometimes it is helpful to have inspectors set aside a group of parts that represent the full spectrum of measurements. Ten samples are considered a good number for a Gage R&R study in a manufacturing environment, but smaller quantities can be used for low volume environments.
5) Ensure samples are not identifiable to the operators
Gage R&R studies require multiple measurements to be taken on the same part, to see if the individual or equipment can repeat itself and repeat others. In order to avoid any human influence, only the person conducting the Gage R&R study should know which sample is being measured. It must be a blind study, so they cannot subconsciously achieve results based on what they remember as the last reading. That is why it is important to have an outside observer conduct and watch the entire Gage R&R study, to avoid these potential issues, which could make the measurement system look better than it is performing in the real process.
What is an acceptable Gage R&R
In order to feel comfortable using the measurement system, the results of the Gage R&R study should prove that the R&R variation is less than 10% of the tolerance range.
Here is the criteria for determining if your measurement system is adequate, using the different % calculations in Minitab (taken from AIAG guidelines for the gage R&R table)
- Less than 10% = ACCEPTABLE – No action required
- Between 10% and 30% = MARGINAL – If Ppk is less than 1.67, then improve measurement process until % of Tolerance is less than 10%, otherwise, no action is required
- Greater than 30% = UNACCEPTABLE – Must improve measurement process so % of Tolerance is less than 10%, or less than 30% with Ppk greater than 1.67
Additional Resources
- NIST Certification / Calibration– creativesafetysupply.com
- Six Sigma Belts– iecieeechallenge.org
- Six Sigma Certification Belts – Is it Worth It?–lean-news.com
- Why Six Sigma Root Cause Analysis is a Great Tool–kaizen-news.com
- Understanding the DMAIC Model– blog.creativesafetysupply.com
- Six Sigma Belts and Their Meaning– blog.5stoday.com
- 5 Things You should Know about Six Sigma Belts– 5snews.com